Choose the Perfect Welder for You
Sure, welding is a specialist skill perfected by tradespeople over many years, but that doesn’t mean you can’t master the basics and do an excellent job on your own projects! All you need is a welder to start with, but as a beginner even that can seem like a chore.
Fear not, we’re going to run through the different types of welding machines so that by the end of this read; you’ll know exactly which one to purchase.
ARC Welding
Arc welding is also simply referred to as stick welding. This is the most basic of all welding types, though it still has a wide range of uses. The welding stick uses electric current to form an arc between it and the metals to be joined. Stick welding tends to be used on thicker metals as it can be exceptionally hot, and isn't considered to be particularly tidy. An arc welding machine can be bought for pretty cheap, and even the most basic of these will be capable of tackling most of the tasks that the home handyman may require it for.
The trickiest part of an arc welder is getting the technique for speed right. You have to move the stick along the piece at a consistent rate, and also feed it into the metal at a constant rate, which varies according to the metal type and thickness.
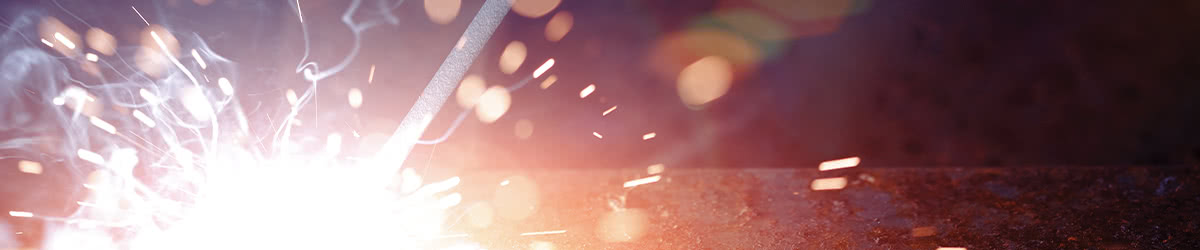
FCAW (Flux-Cored Arc Welding) - Gasless
This is essentially the gasless version of MIG welding, and most MIG machines can be used this way. A special tubular wire filled with flux can be fitted in place where normal MIG wire goes, and when the welder is in action; the flux heats up to create a gas which shields the weld.
It is well-known for being extremely inexpensive and easy to learn, just like normal MIG welding. However, the lack of a steady supply of shielding gas often contributes to a very messy weld, and so it has quite limited practical use in the automotive industry.
MIG and MAG Welding
MIG welders and MAG welders are probably the most commonly used types of welding in automotive fabrication and bodywork. So what is the difference between MIG and MAG welding? They are essentially the same, but while MIG stands for Metal Inert Gas; MAG stands for Metal Active Gas.
In both of these welding processes, a shielding gas is supplied to the tip of the handpiece, where wire is fed from a spool when you pull the trigger on the welding gun. The wire carries a high current, which both heats up the two metals to be joined; and melts to add to the weld pool as well. The gas prevents contamination of the weld pool. A constant voltage and direct current power source is required for this method, with most lower cost machines able to run happily on standard home power supplies.
The MIG process uses only inert gases such as Argon and Helium, and is primarily used to weld aluminium. MAG welding generally uses a mixture of Argon and CO2, sometimes along with a percentage of Oxygen. This active shielding gas interacts with the weld pool to both shield it, and to control the temperature, penetration and the amount of splatter.
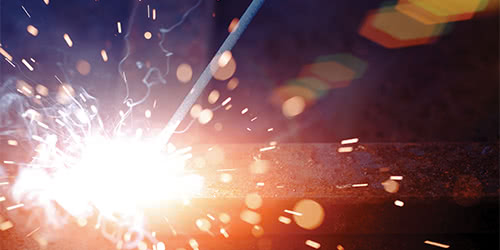
A MIG or MAG welder is a little more sophisticated than the ARC welder, and will cost accordingly. There’s also the cost of gas bottle rental and refills to factor in, and while a MIG welder can be used gasless with a flux core wire; it won’t easily achieve the same weld quality.
As far as useability goes, the machine feeds into the metal for you, so that’s one less thing the beginner needs to concentrate on. Once you’ve played around with some practise welds and dialled in the right wire speed and current; it’s pretty straight forward.
TIG (Tungsten Inert Gas) Welding
A non-consumable tungsten electrode is used in this type of welding process. This tungsten electrode is made use of to heat the base metal and create a molten weld puddle. A shielding gas is also applied, to prevent weld contamination. Generally, a TIG welder is employed to carry out high quality work when a superior standard finish is required, without making use of excessive clean up by sanding or grinding. Think about those tidy welds you see on a stainless steel exhaust system, or custom intake manifold.
This is often considered to be the most advanced type of welding. The equipment is expensive, and the skills take a while to master. This machine is one to purchase once your welding skills are beyond what the MIG or MAG can deliver, and you want to take it to the next level.
Gas Welding / Oxy-Fuel Welding
It's probably more common to see an Oxy-fuel torch used to cut metal rather than weld it, but it is possible to weld metals with the right type of torch. Oxy-Fuel welding used to be the most common type of welding, but it has long since been superseded by other types. Now Oxy-Acetylene torches can be occasionally seen in use when brazing things like copper or brass, but their use as welders is pretty rare.
Now, get out there and weld!
So, with your options all laid on the table, which will it be? Pair your new welder with a handy flip up helmet, maybe some fancy welding clamps; and you’ve just opened up a whole new world of DIY projects and repair jobs in your own shed.
*Important information* - Click here to read more about our DIY Advice Terms and Conditions.