How To Replace Brake Rotors
Overview
Speed limits mean it doesn’t really matter how fast your car can go or how quickly it can get there. However, stopping is another matter. The braking system is the critical to the safety of your vehicle, yourself and your passengers.
Over time brake rotors wear out. They may crack or develop deep score marks, warp or simply wear out. When this happens they need to be replaced.
Items
Materials
- Replacement Brake Rotors
- Lubricant, WD40, Inox etc
- Tie Wire
Tools
- Vehicle Jack
- Car Stands
- Spanner Set
- Socket Set
- Screwdriver
- Wire brush or oil stone
Steps
Raise Vehicle
Start by raising the vehicle.
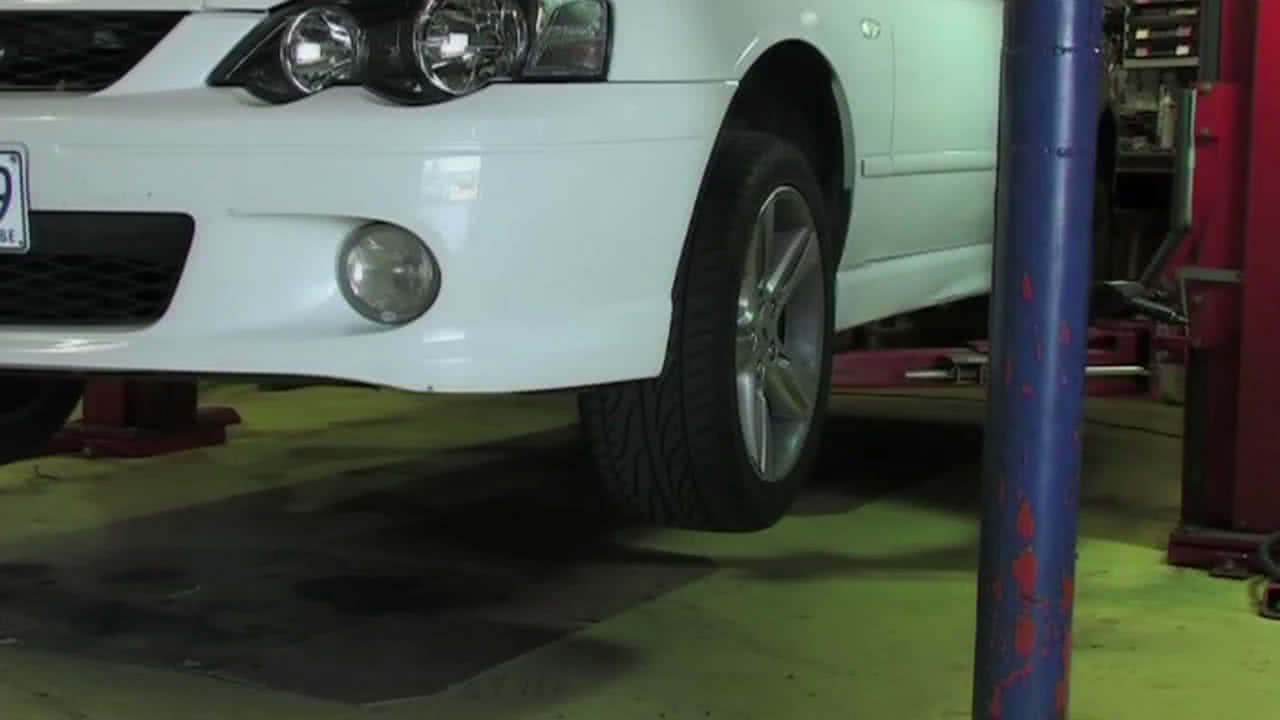
Remove The Wheel
Next, unscrew the wheel nuts and remove the wheel.
The wheel may be difficult to remove due to a rust scale build up around the hub ring.
Removing the wheel will give you clear access to the brake rotor, caliper and spigot.
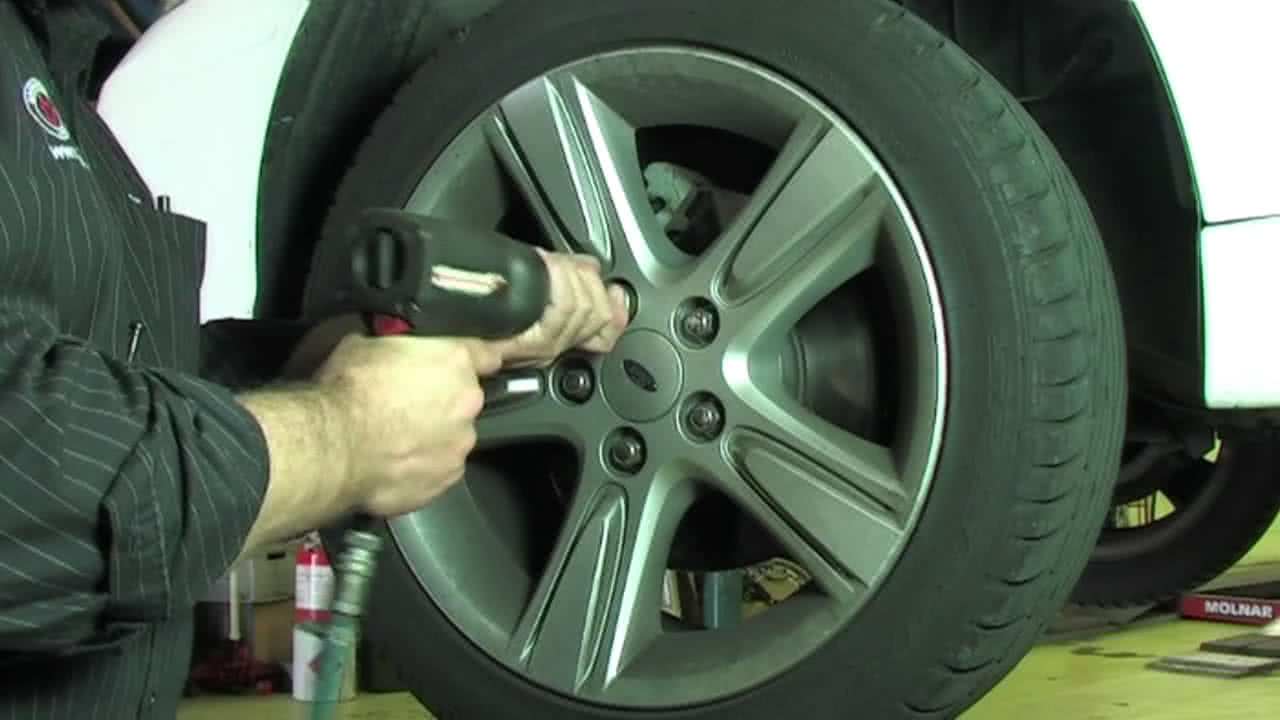
Remove Brake Pads And Caliper
You’ll need to remove the brake caliper.
Loosen and remove the retaining bolts and lift the caliper away. The caliper may grip a little tightly so don’t force it.
Note: Hanging the caliper by the brake hose will cause damage. Use a hook to secure the caliper to a solid part of the suspension.
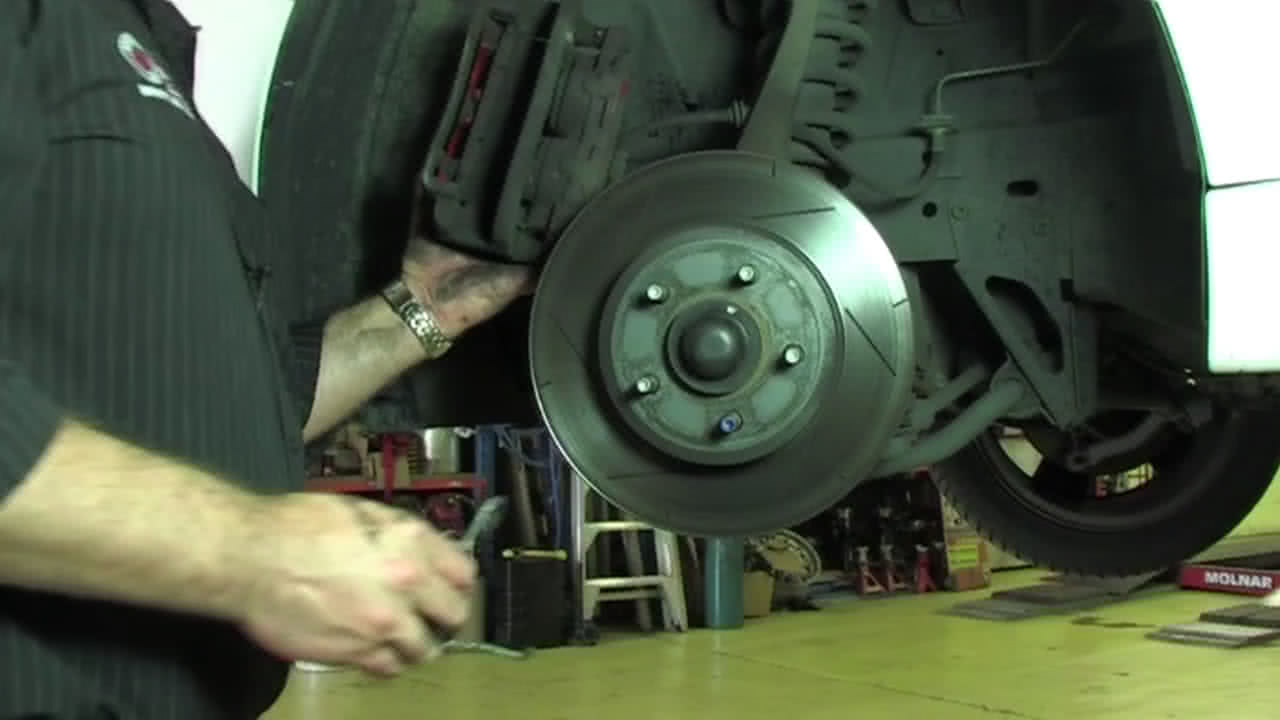
Remove The Brake Rotor
Remove the brake rotor from the hub assembly. Apply firm pressure, as the rotor may be awkward to remove.
Note: This is caused by rust scale build up on the inside of the brake rotor and the hub surface. It is extremely important to remove the rust scale build up before fitting the new disc.
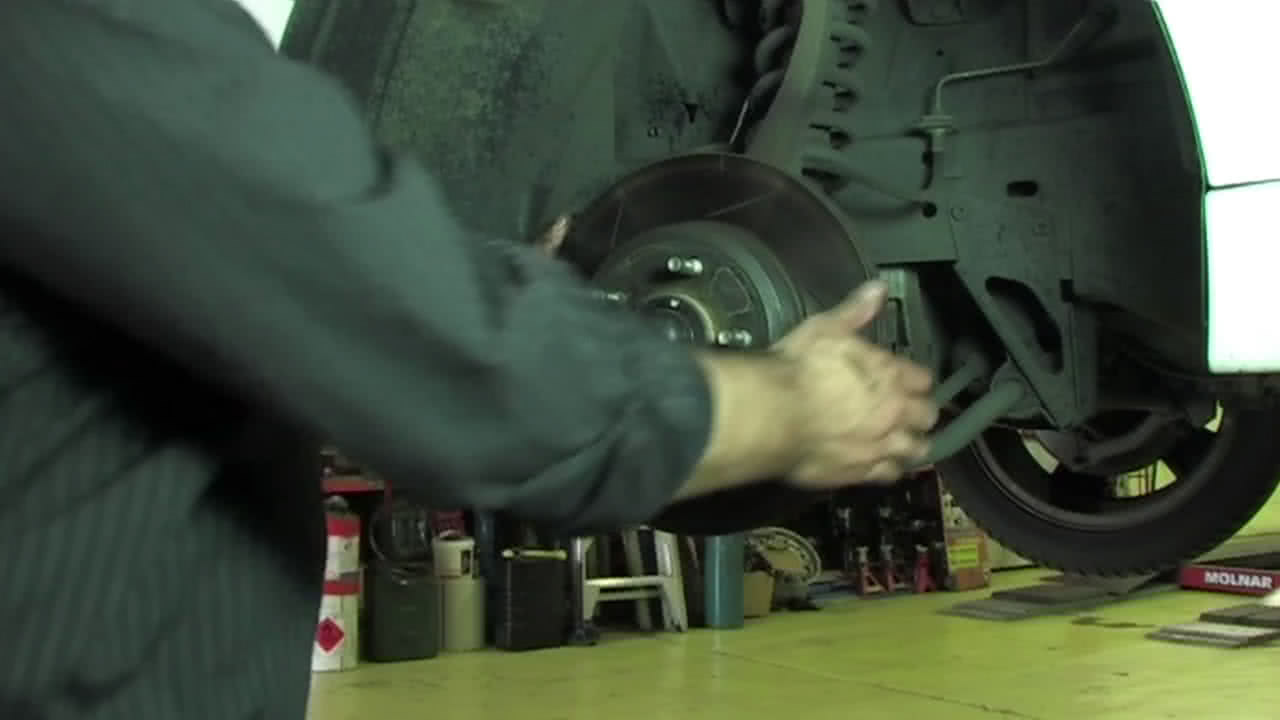
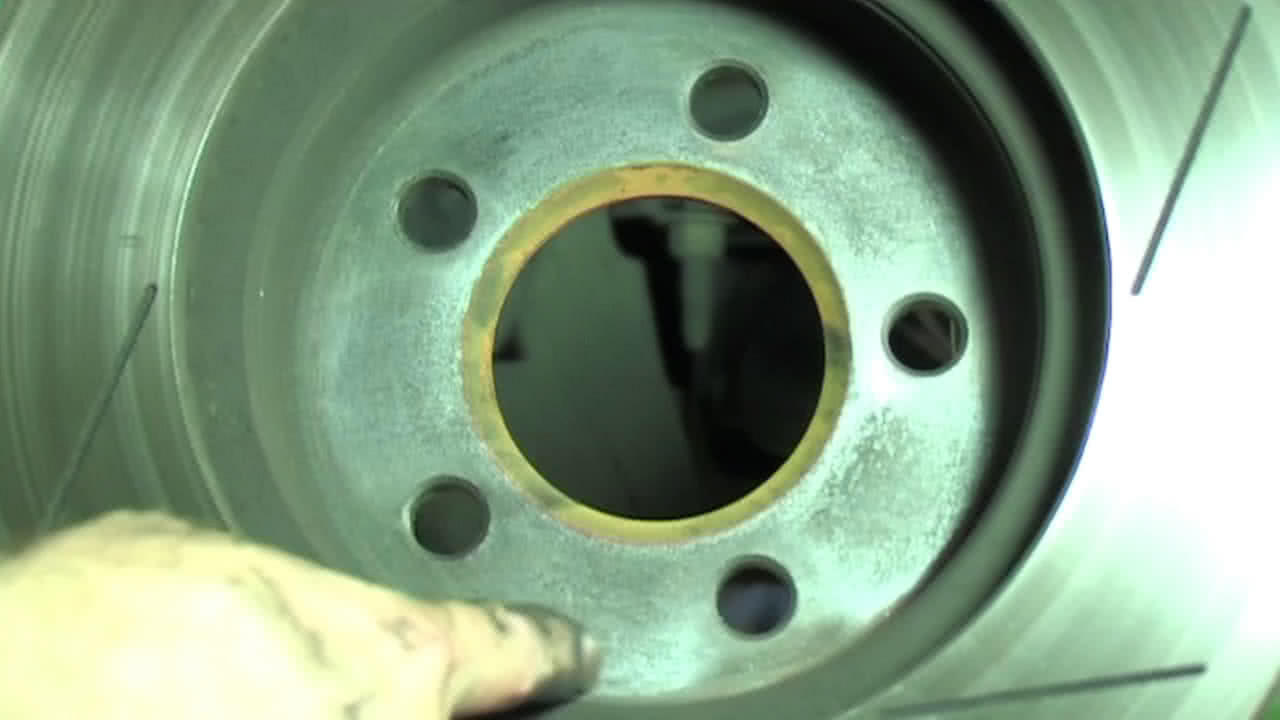
Prepare Hub Surface
To do this, spray the hub with a lubricant such as WD40 or Inox.
Then use course sandpaper to begin removing the rust scale from the hub surface. Once most of the rust has been removed switch to an oil stone to remove the remaining rust scale. Even the slightest bit of rust can cause the disc to mount incorrectly causing excessive run out, so make certain the hub is clean.
Note: Excessive run out is where the disc doesn’t rotate smoothly and gets trapped between the brake pads.
Using the oil stone, make sure you clean around each wheel stud carefully to ensure the new brake rotor sits perfectly.
Using a rag wipe away the lubricant.
Check the hub carefully for any spots of rust scale that haven’t been removed and clean them off. When the machining marks on the face of the hub are visible the hub is clean.
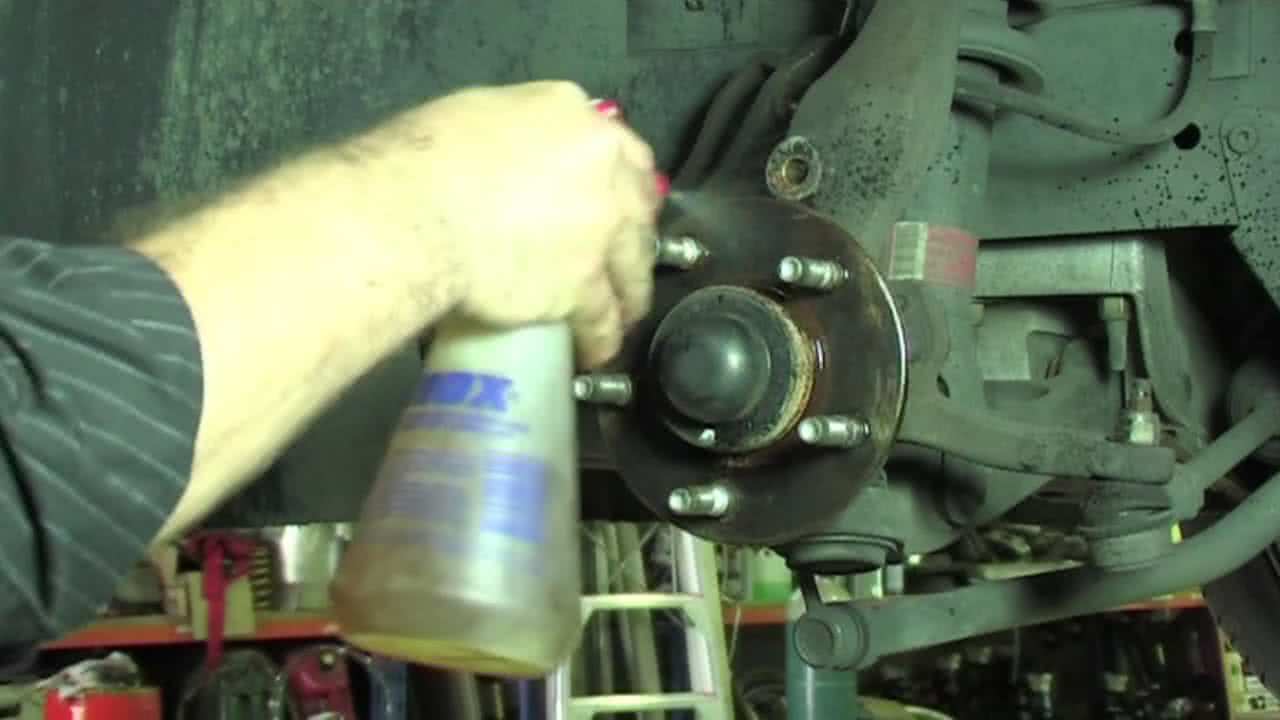
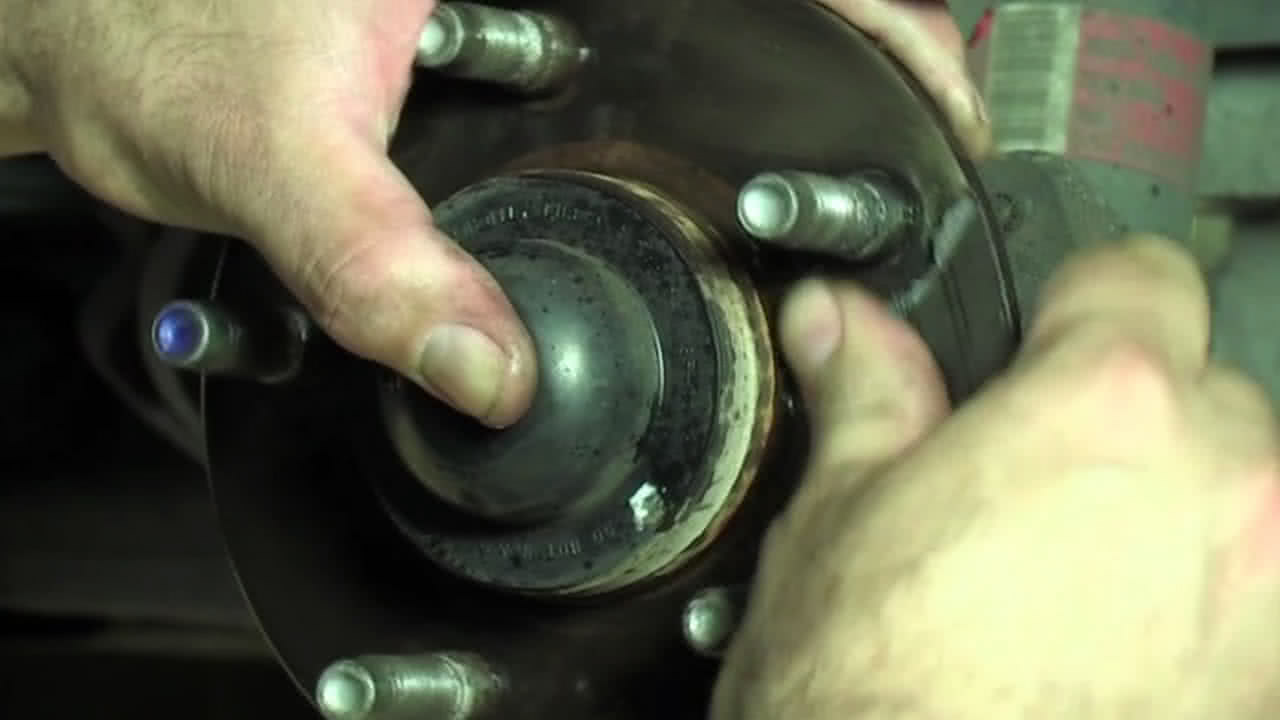
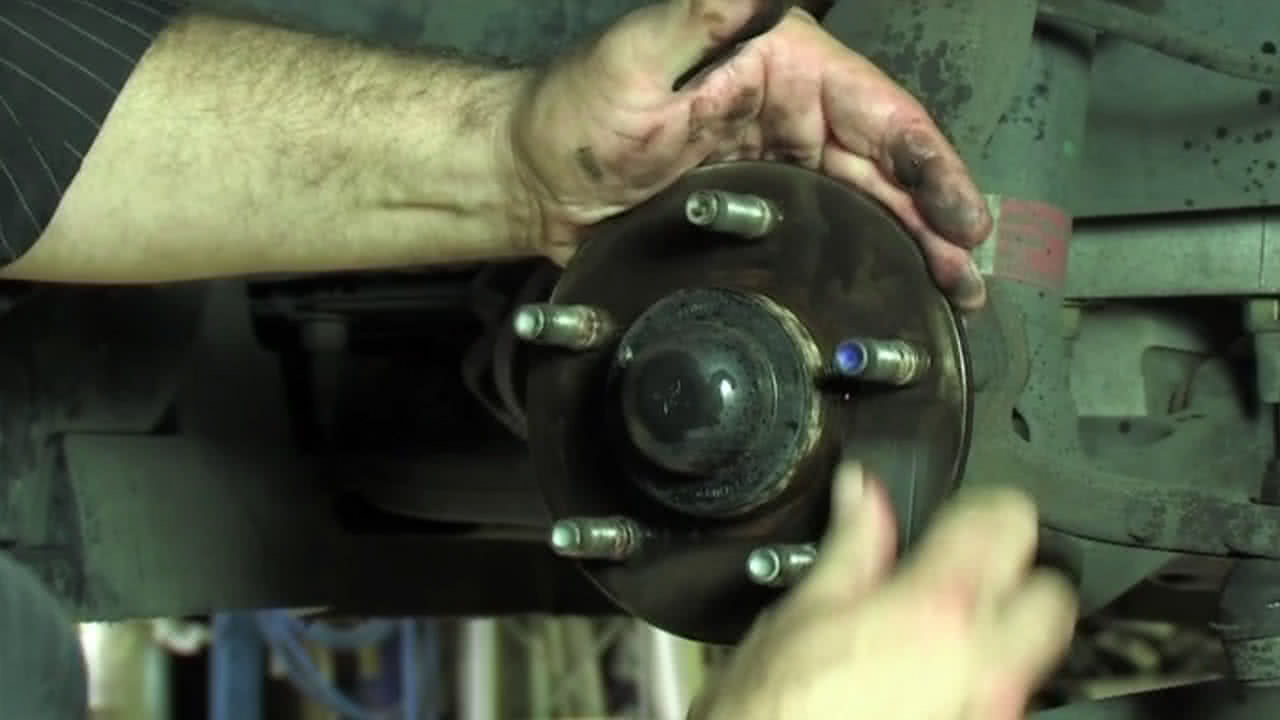
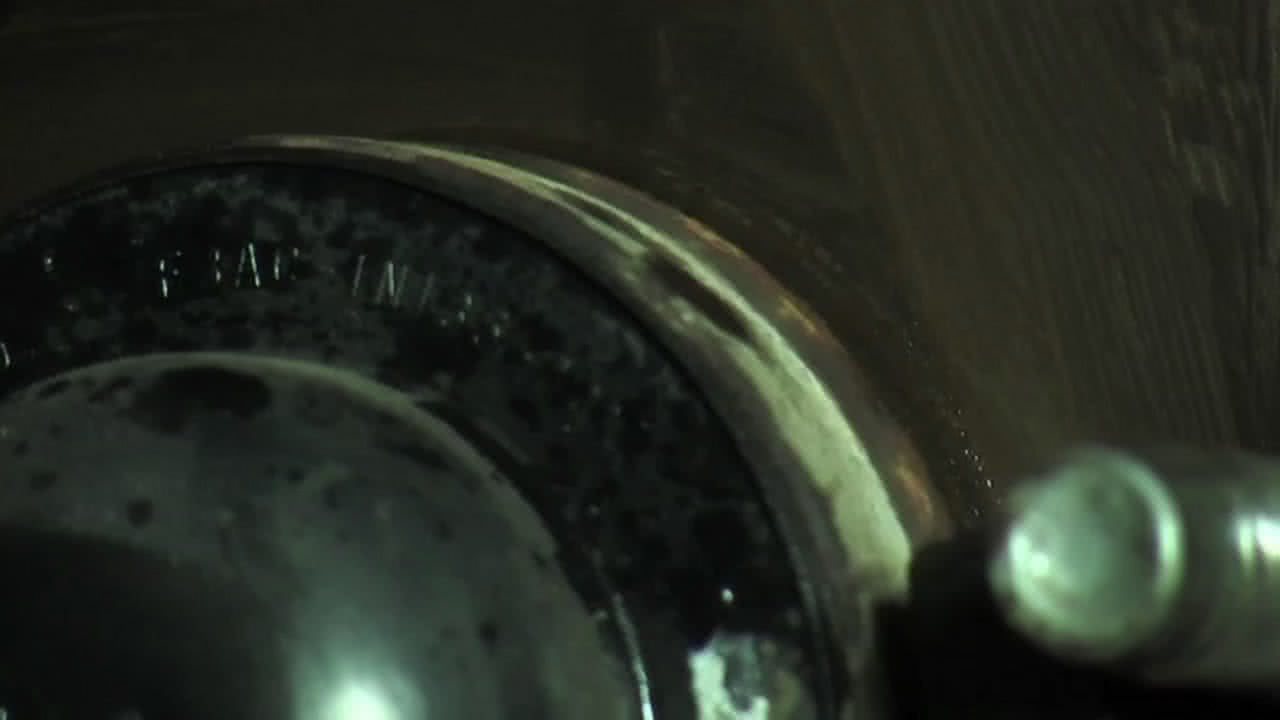
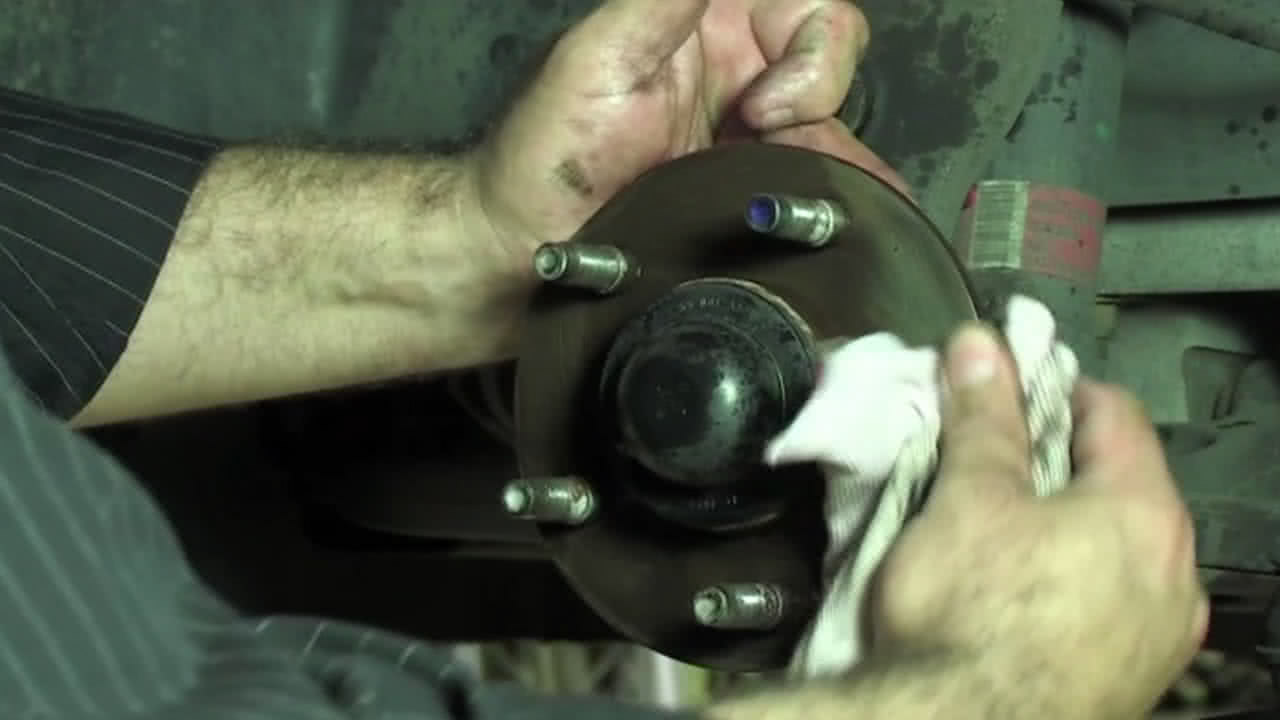
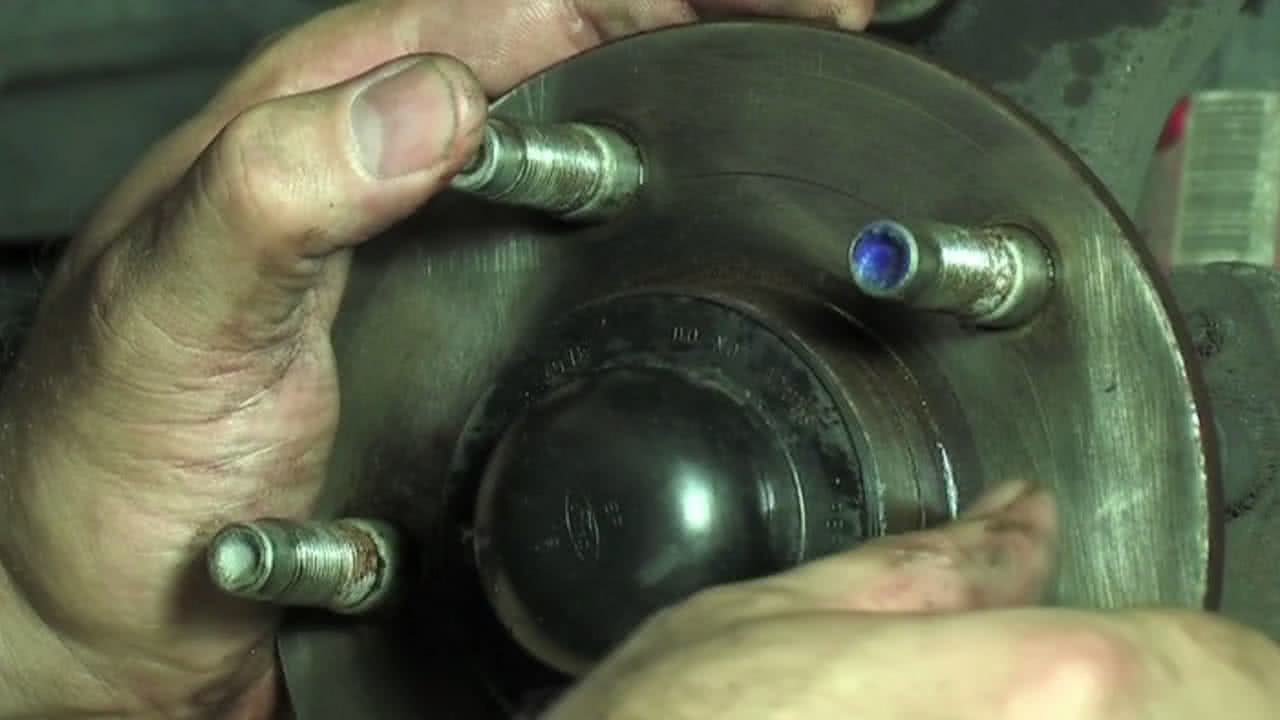
Clean Hub Spigot
Using fine grade sand paper, is to clean the hub spigot. Incorrect cleaning of the spigot can cause the rotor to sit away from the hub surface.
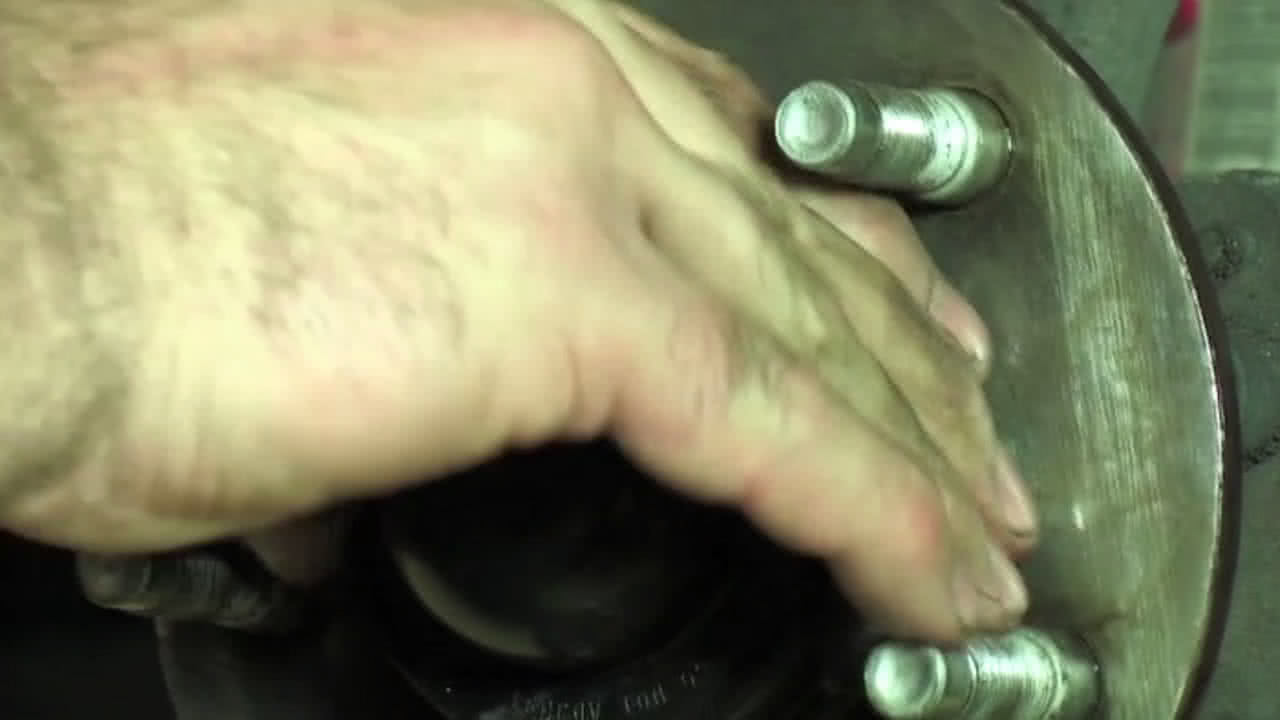
Reset Pistons Inside Caliper
To make room for the new disc the pistons need to be pushed back inside the caliper.
Clamp the brake hose securely
Attach a spanner to the bleed screw
Attach a hose and suitable storage container
Use a pad spreader to take up the compression load
Use the spanner to loosen the bleed screw, you will see brake fluid pass through the hose into the container.
Continue using the spreader to force the brake fluid out and pistons back into the caliper.
Once the pistons are fully retracted you can remove the hose. Make sure you tighten the bleed screw first to prevent air getting into the brake system.
You can then remove the pad spreader.
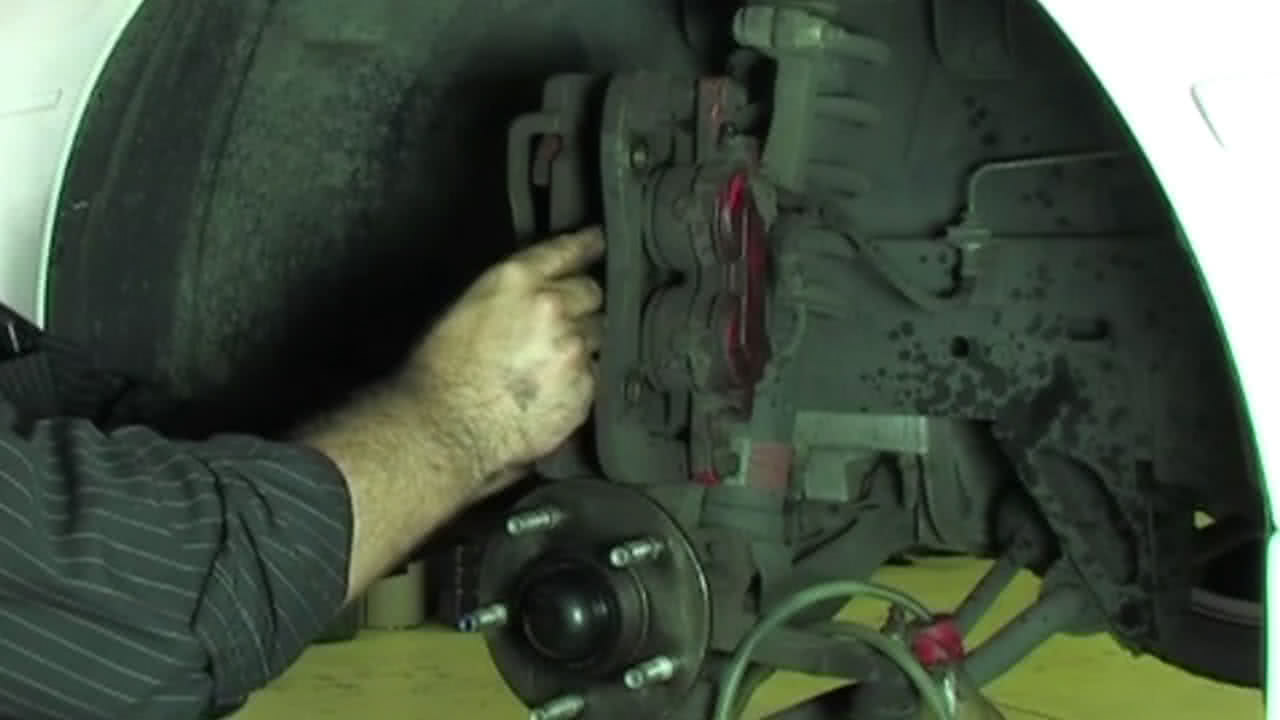
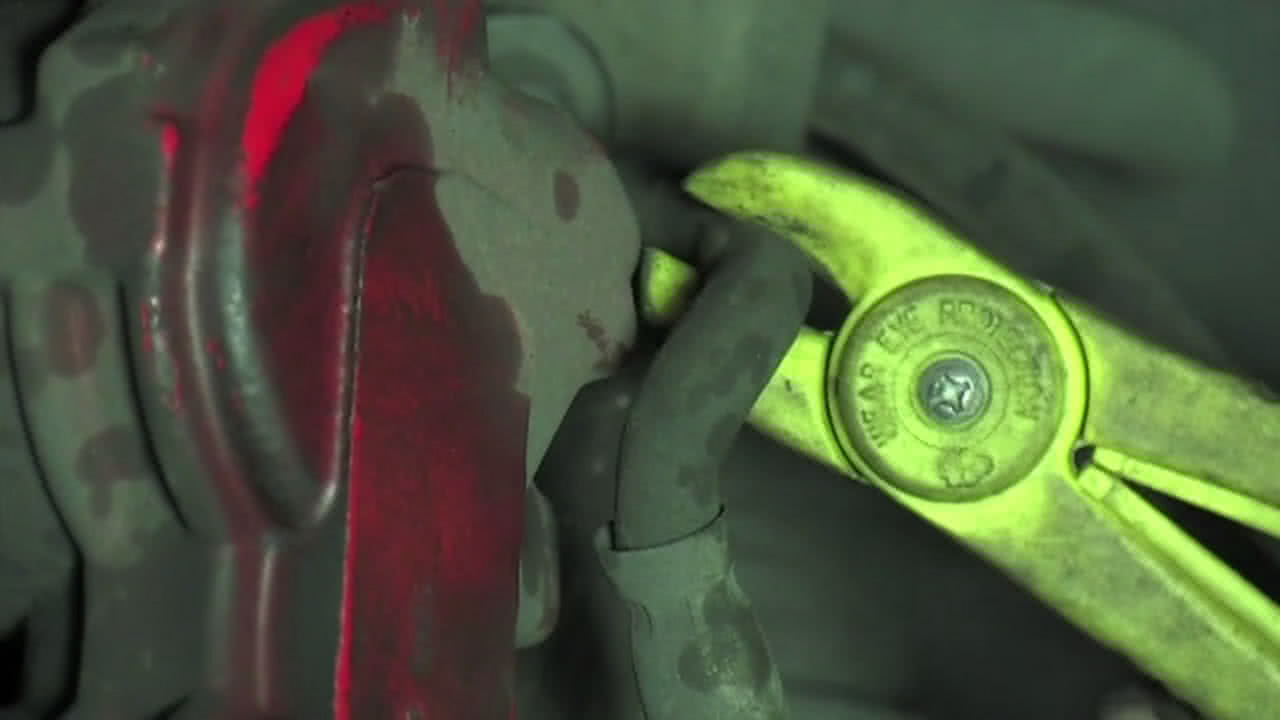
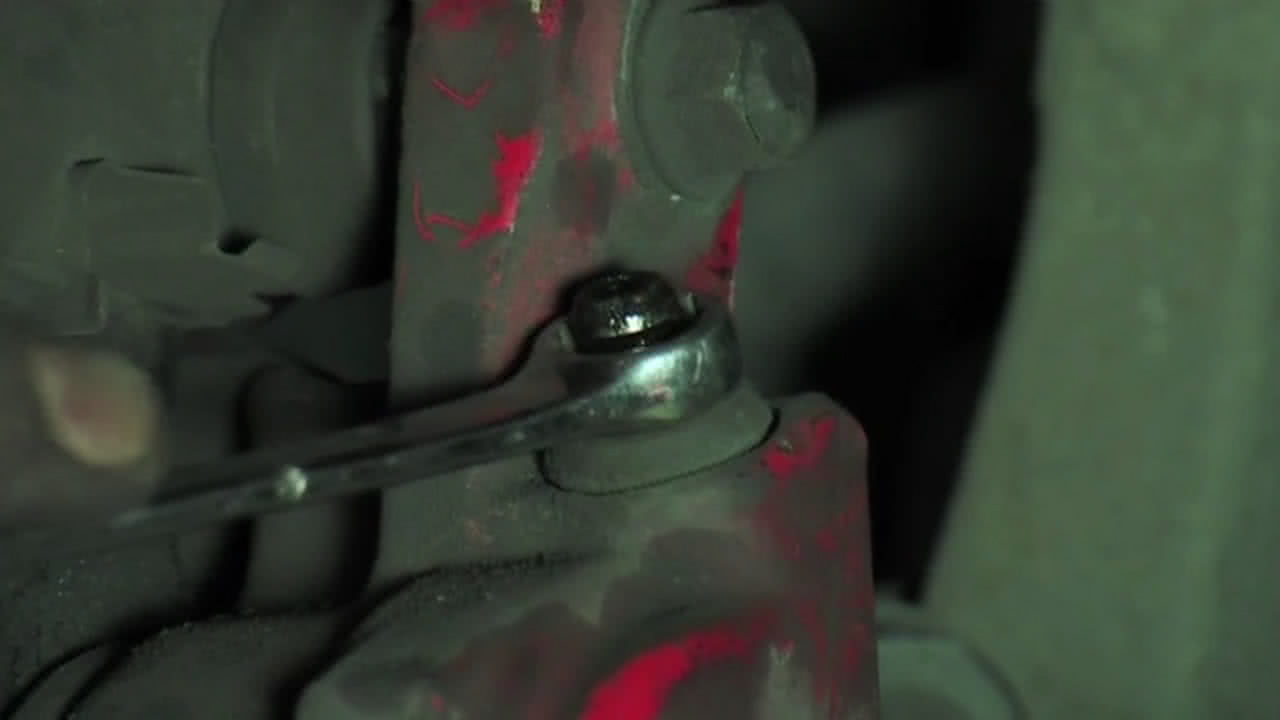
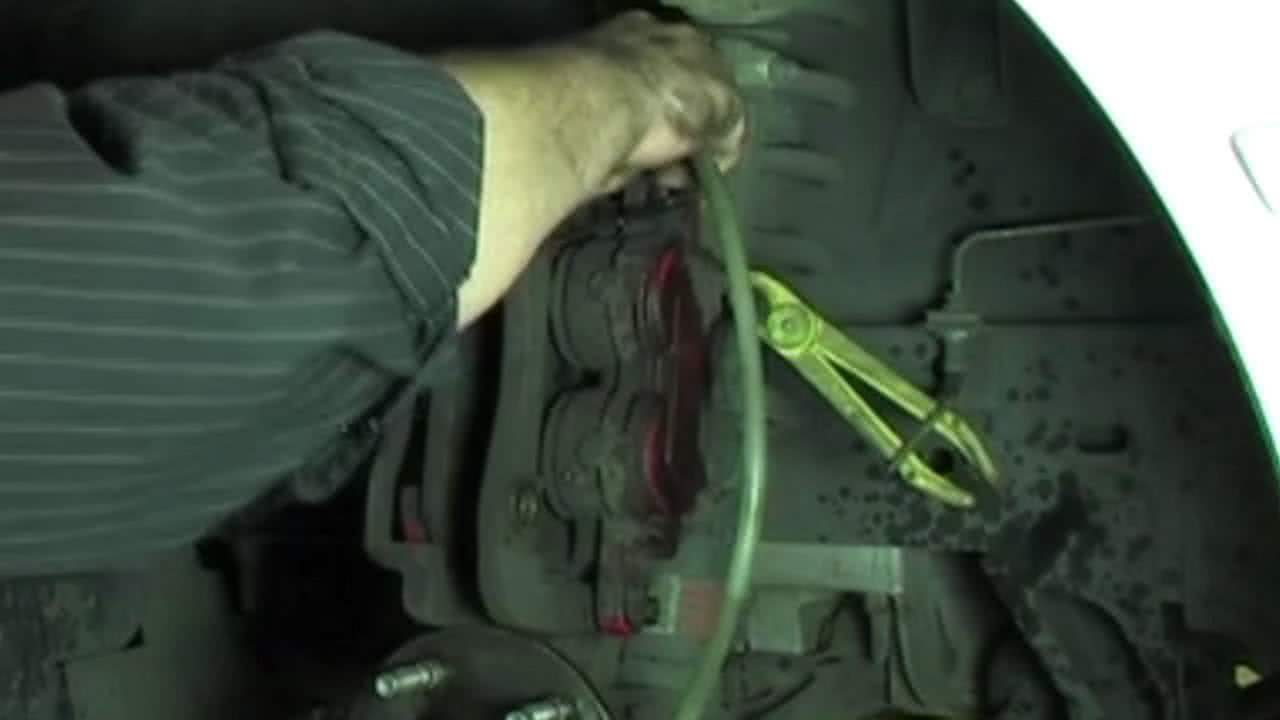
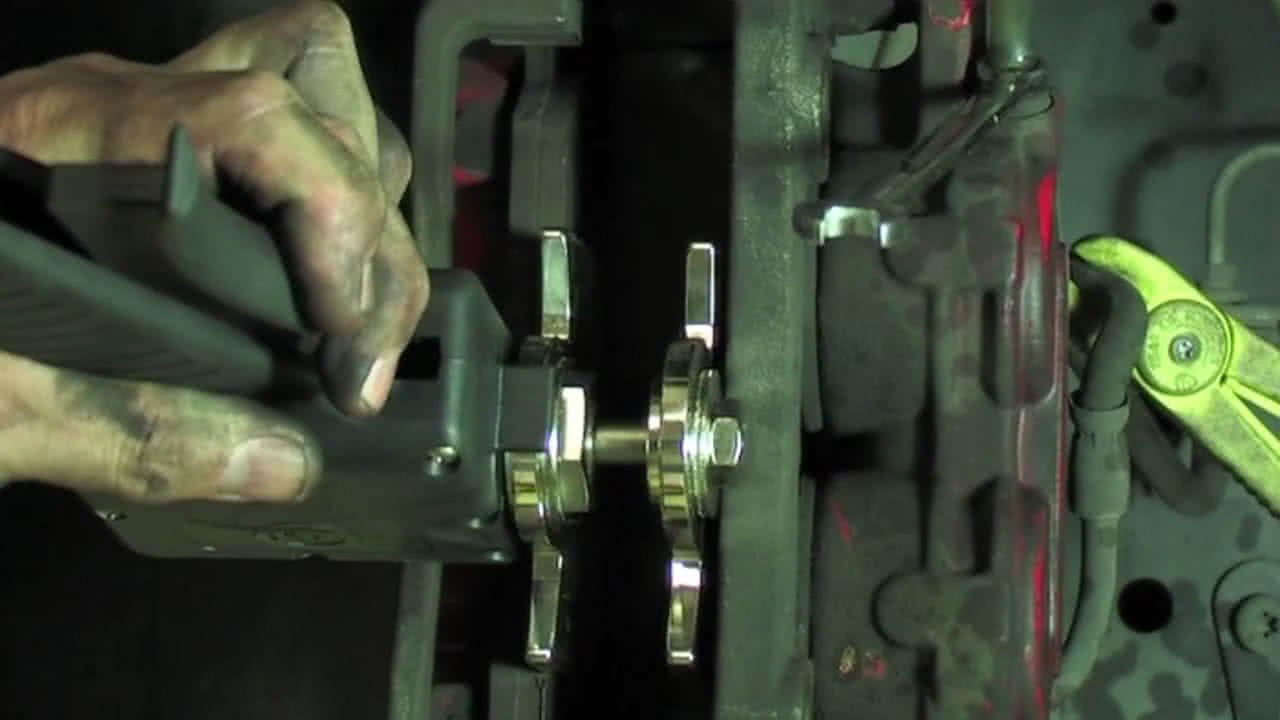
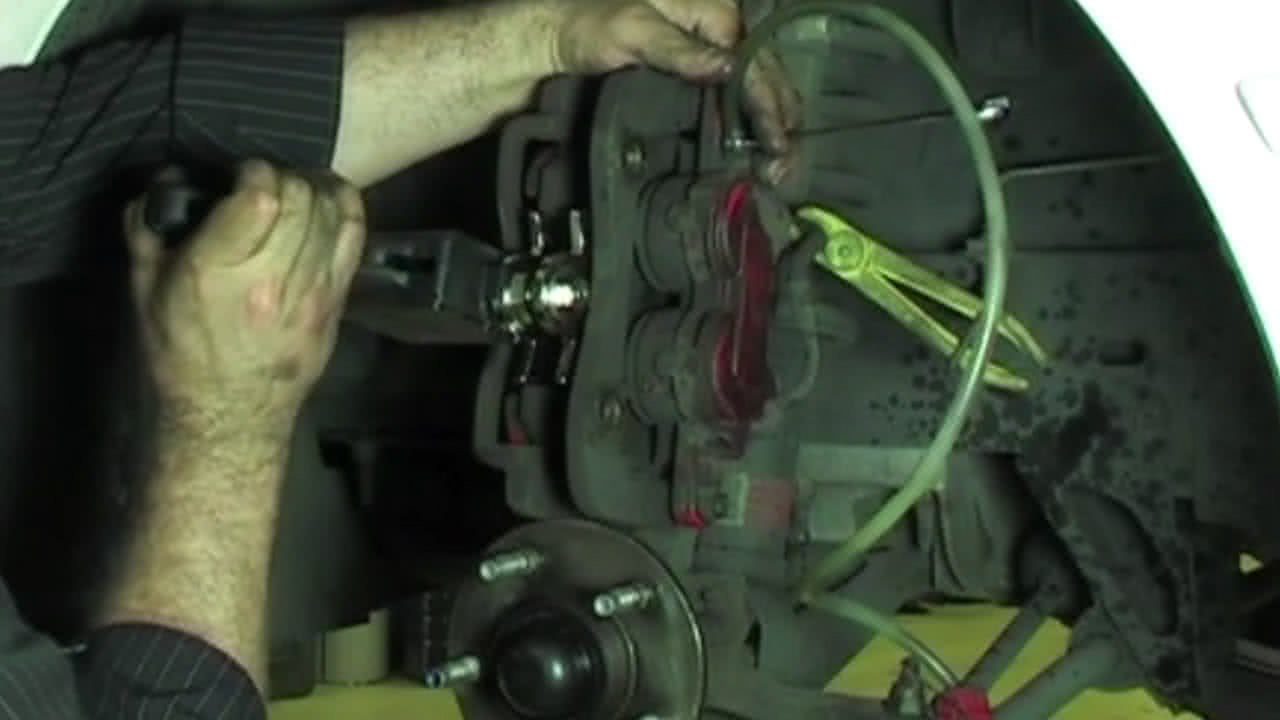
Clean The New Brake Rotor
Clean the friction faces of the disc using a brake-cleaning agent. Never use a petroleum or silicon based cleaner such as degreaser as it will cause paint damage.
Spray brake cleaner onto a clean cloth. Be careful not to touch the painted surface on the disc. The paint is designed to cure at high temperatures and is extremely easy to damage.
Turn the brake rotor over and clean the hub mounting on the rear of the disk. With all the work you put into the hub, the last thing you want is to attach a dirty brake rotor.
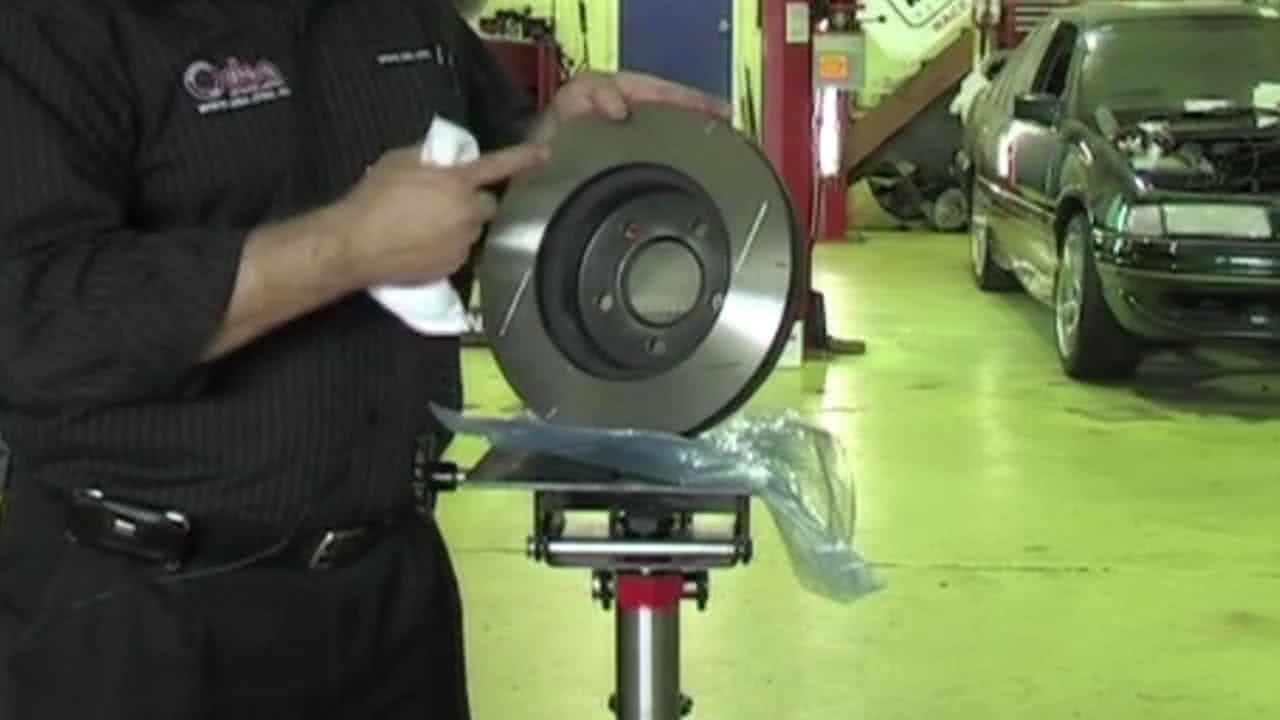
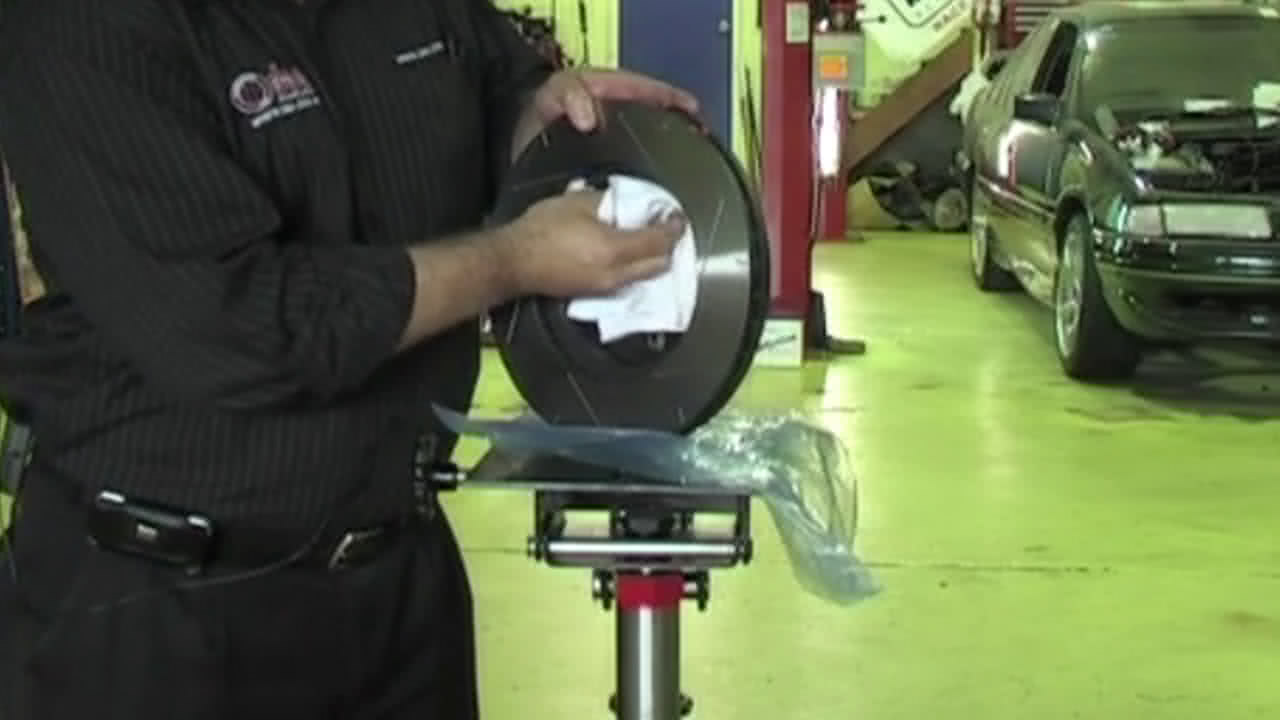
Attach The New Brake Rotor
Using three wheel nuts and washers fit the rotor securely to the hub.
Using the dial indicator measure the run out again with brake rotor attached. A reading over 0.05mm means an incorrectly fitted brake rotor.

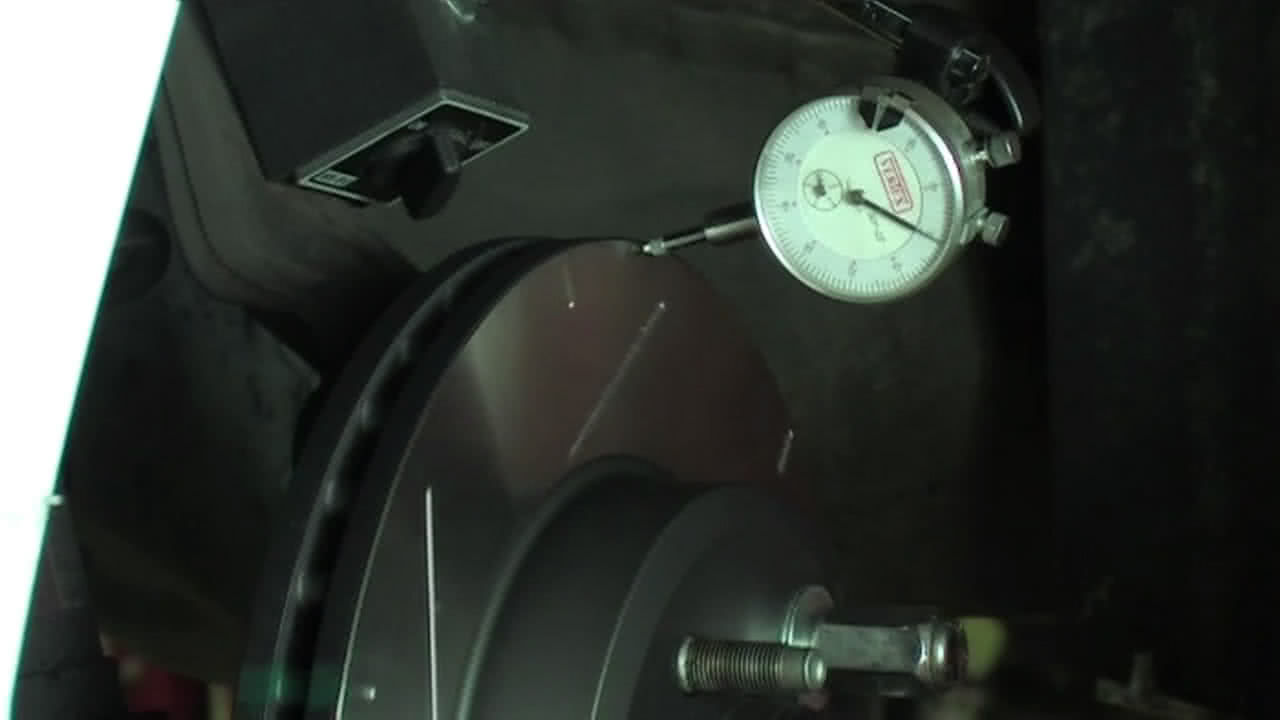
Refit Caliper & Wheel
Refit the caliper over the new brake rotor and tighten to the correct torque using a torque wrench.
Using the oilstone, clean the rear face of the wheel to ensure an even clamping pressure on the disc when the wheel is fitted.
Finally, refit the wheel to the correct torque. Attach the nuts in a cris cross pattern to ensure even pressure.
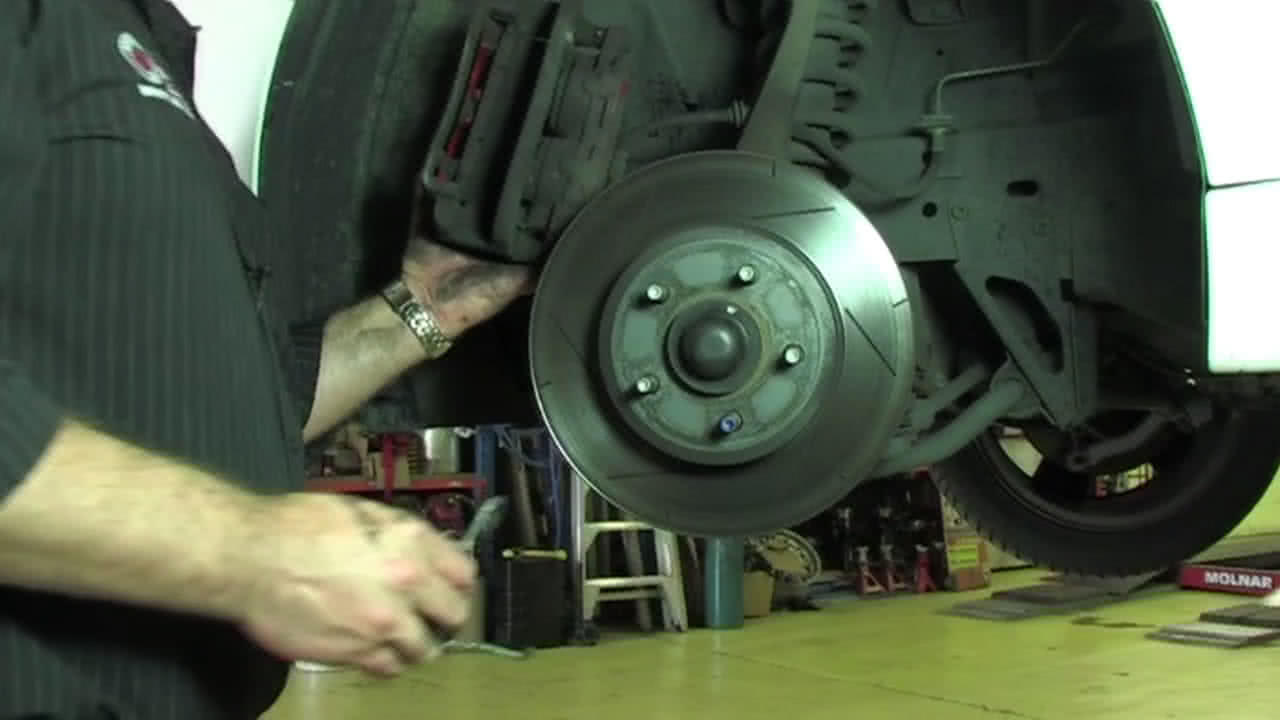

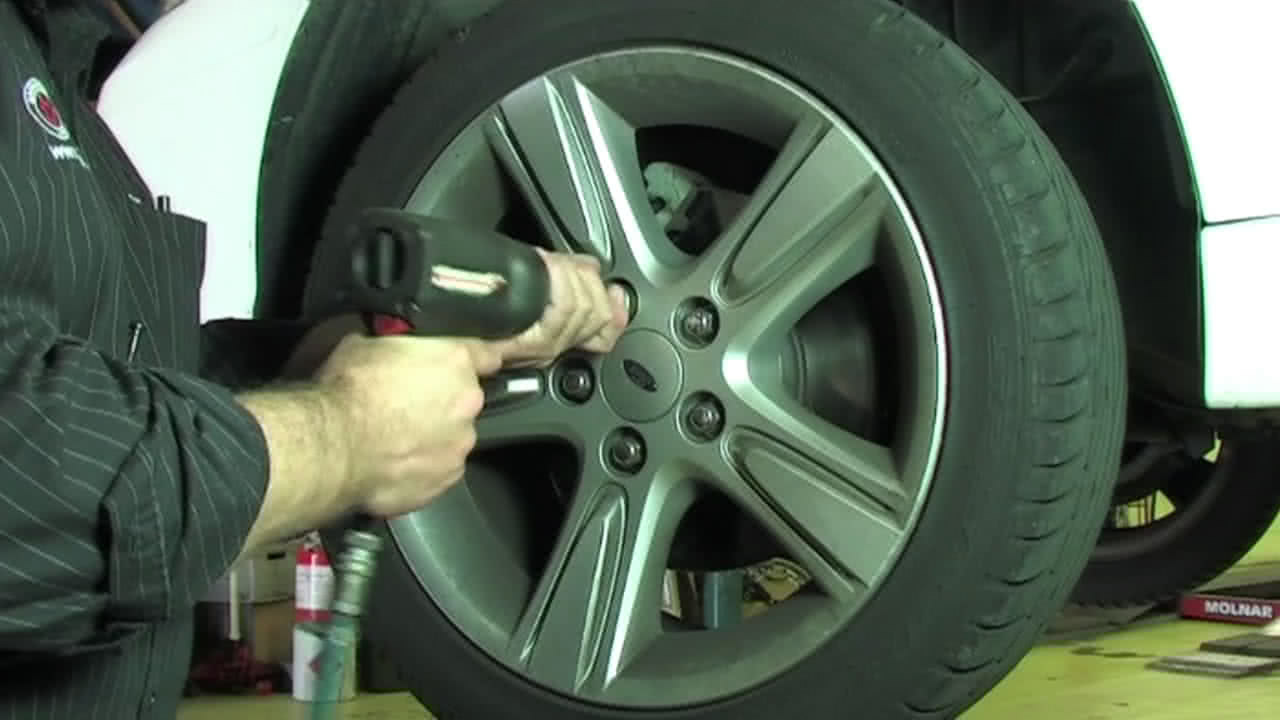
Test Drive
Test drive the vehicle to ensure correct operation of the braking system.
Tips
- Brake rotors are a vital component of the braking system, ensure you double check your work before you commence a test drive.
*Important information* - Click here to read more about our DIY Advice Terms and Conditions.